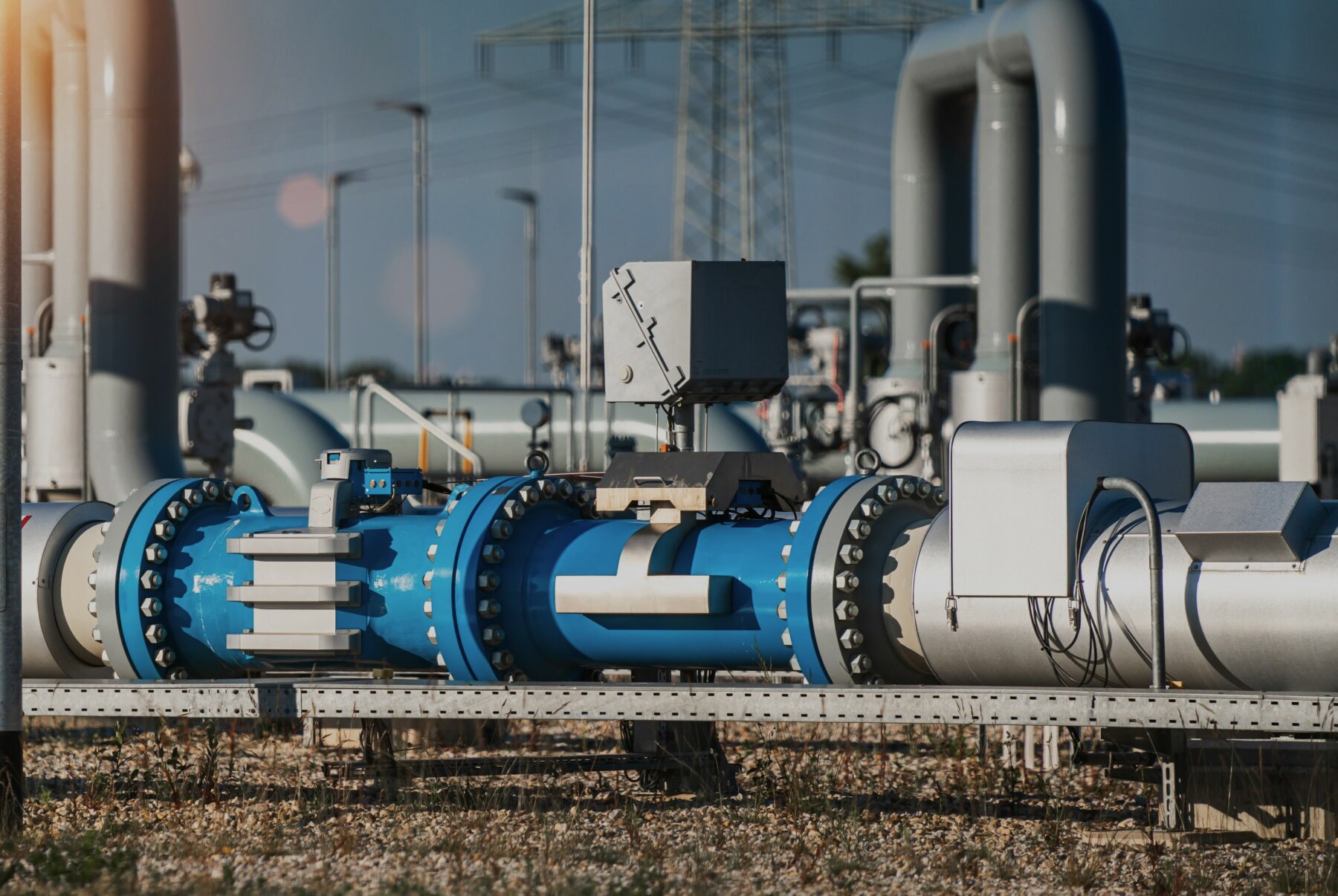
Our mission
Hydrogen and heat transfer, an inseparable combination
We assume that you share our conviction that green hydrogen will play a significant role in the energy transition. Developments in the field of hydrogen are rapid, with the number of installations and electrolysers increasing rapidly worldwide. But the processes are not yet fully defined. Understandably so! People all over the world are looking for the optimum configuration to produce hydrogen as sustainably and efficiently as possible. In the field of heat transfer, Kapp knows the way; we have a suitable heat exchanger for every step in the production of hydrogen. This real edge benefits our customers. That said, knowledge and experience of other experts in the hydrogen sector are essential for us. Our approach in this market is therefore: “Here to teach, here to learn”. A philosophy that stems from the realisation that time passes quickly and that we can accelerate developments, especially together with other experts from the sector.
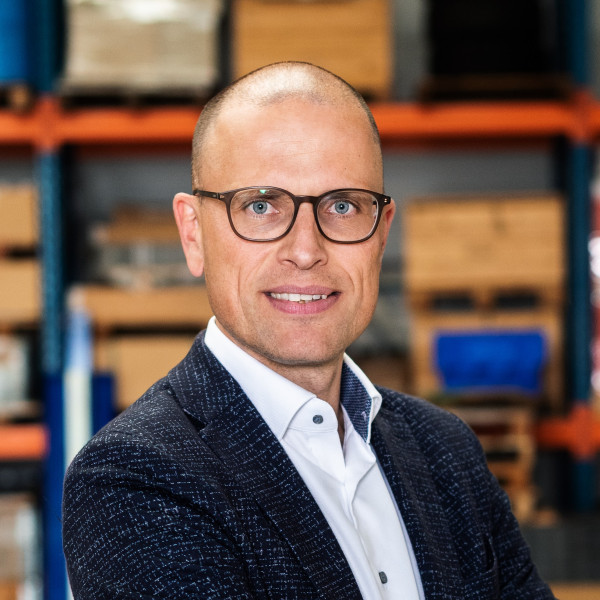
Our approach in this market is therefore: “Here to teach, here to learn”.
JEROEN VAN RUITENBEEK – General Manager Kapp
WHAT WE PROMISE
Our solutions
This is how we can improve your hydrogen process
Sustainable generated electricity is a prerequisite for producing green hydrogen. Keeping this fundamental aspect in mind, we tackle every challenge that arises during the hydrogen production process. Heat exchangers play a crucial role in each step of this process. With our extensive experience and expertise, we are well-versed in the associated challenges and have the most suitable heat exchangers for every step. Furthermore, we possess a unique advantage in compression and purification sub-processes, with our highly compact heat exchangers. If you require further information, we would be delighted to provide it.
WHERE WE ARE UNIQUE
Perfect fit for the hydrogen process
Hydrogen is the smallest molecule. In hydrogen production, it carries risks. In a number of processes in hydrogen production, pressures are high, and leakage can be disastrous; hydrogen and oxygen flows are explosive. In such critical processes, the right equipment is vital, even literally. For hydrogen processes, large, traditional tubular heat exchangers are still often considered because of their robustness. Sometimes this is a fine solution, but even more often other techniques are better suited. And there are plenty of examples where our all-welded plate heat exchanger is practically the only suitable solution. We see cases where our solutions weigh 70% less, cost 50% less, recover more heat and are at least as robust as the traditional tubular heat exchanger. For various processes in hydrogen production, a Plate & Shell heat exchanger is the perfect, and in some cases the only suitable, technology. A Plate and Shell heat exchanger is:
- Very compact – so a smaller plot size, less civil-work, insulation, piping, etc.
- Suitable for high pressures.
- Fully welded and therefore safe for hydrogen application and guaranteed leakproof.
- More profitable thanks to lower CAPEX and OPEX
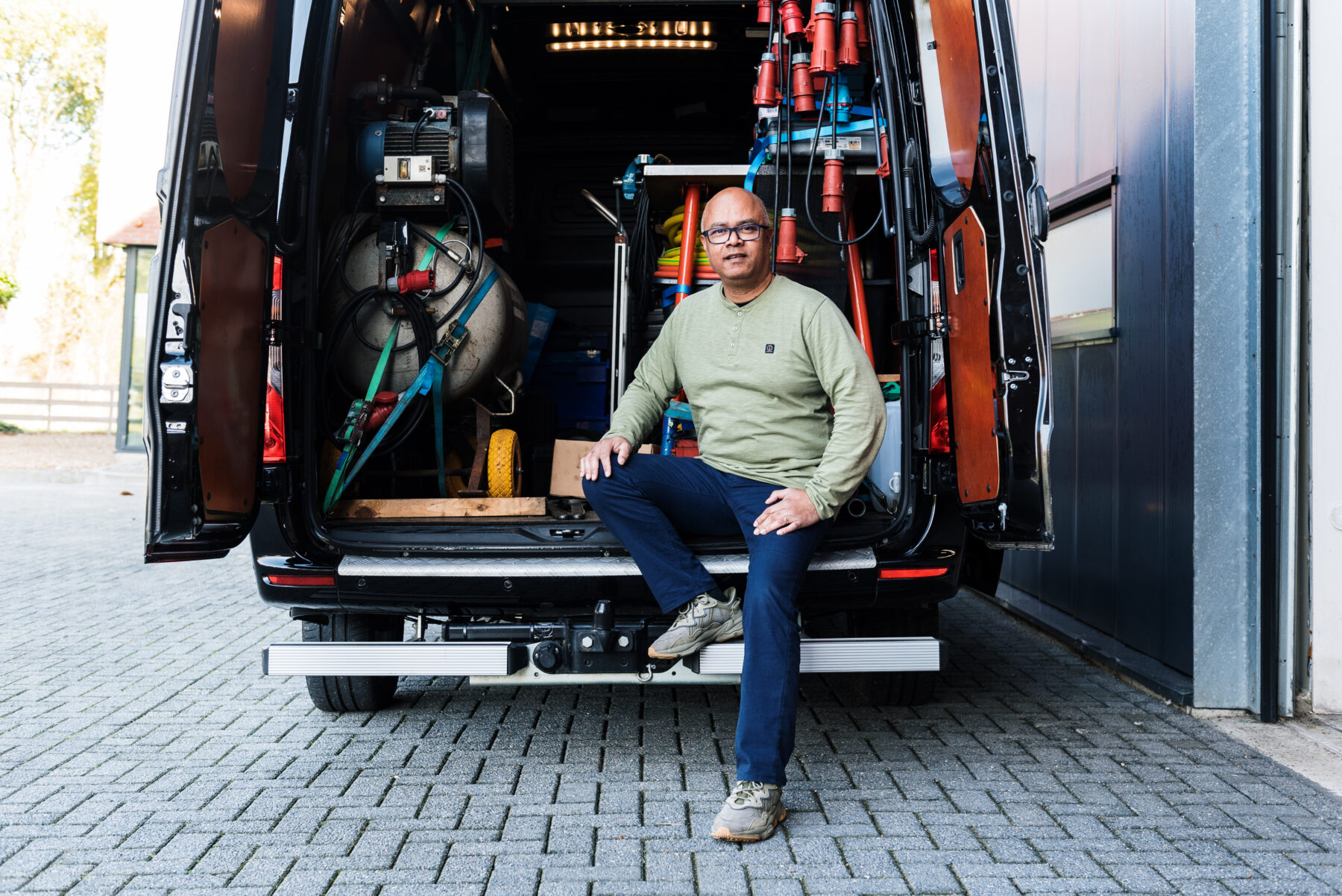
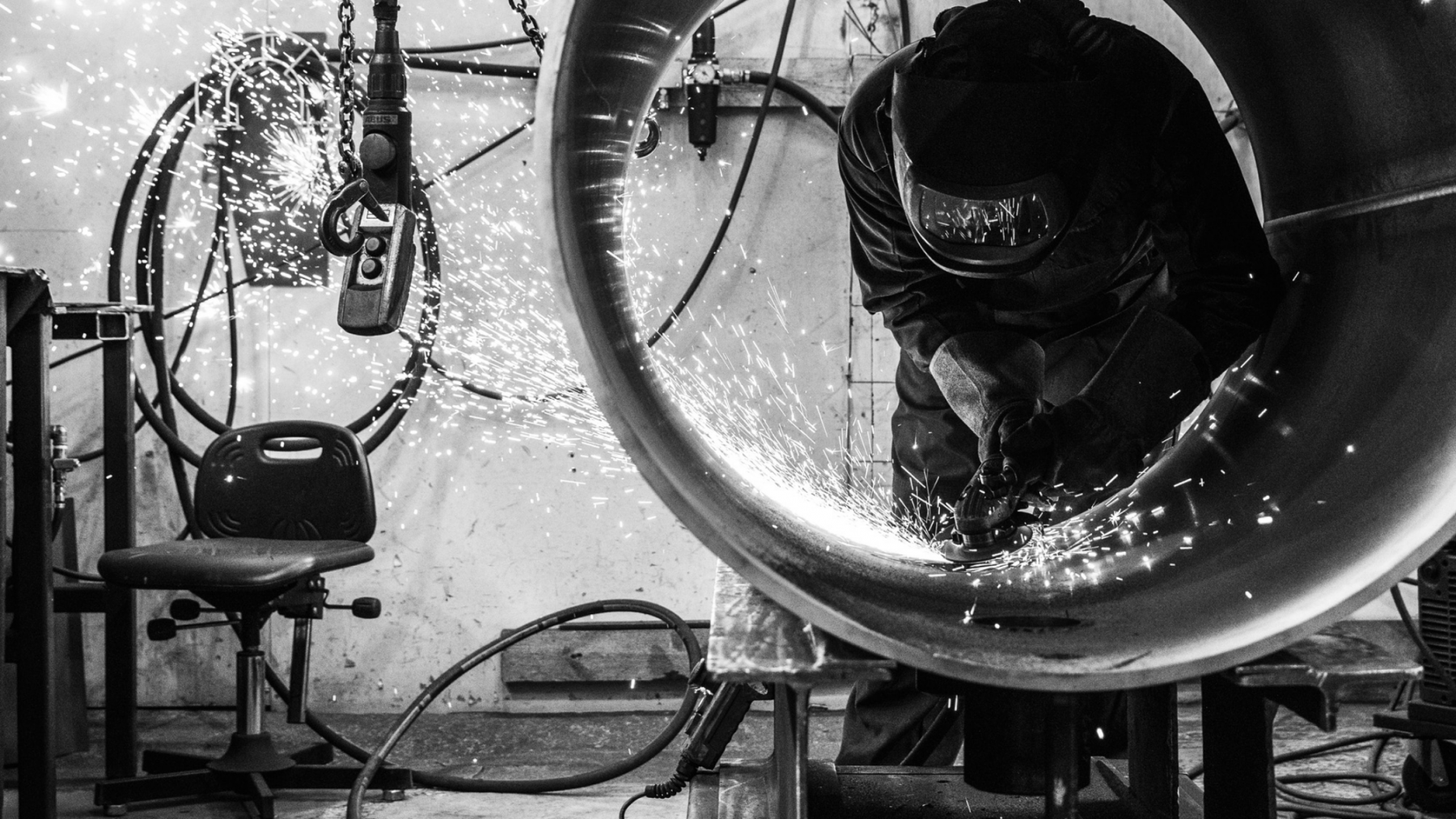
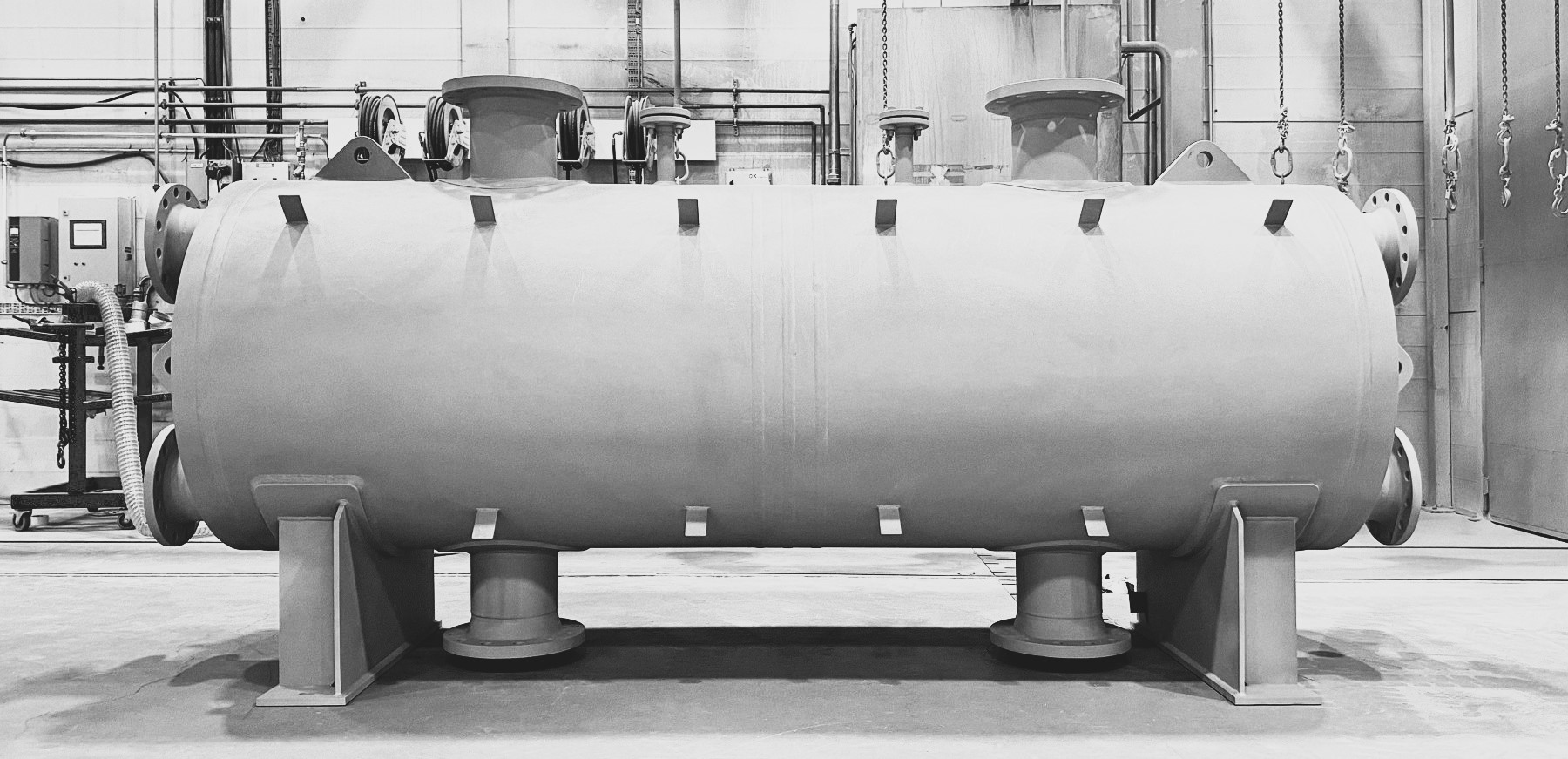
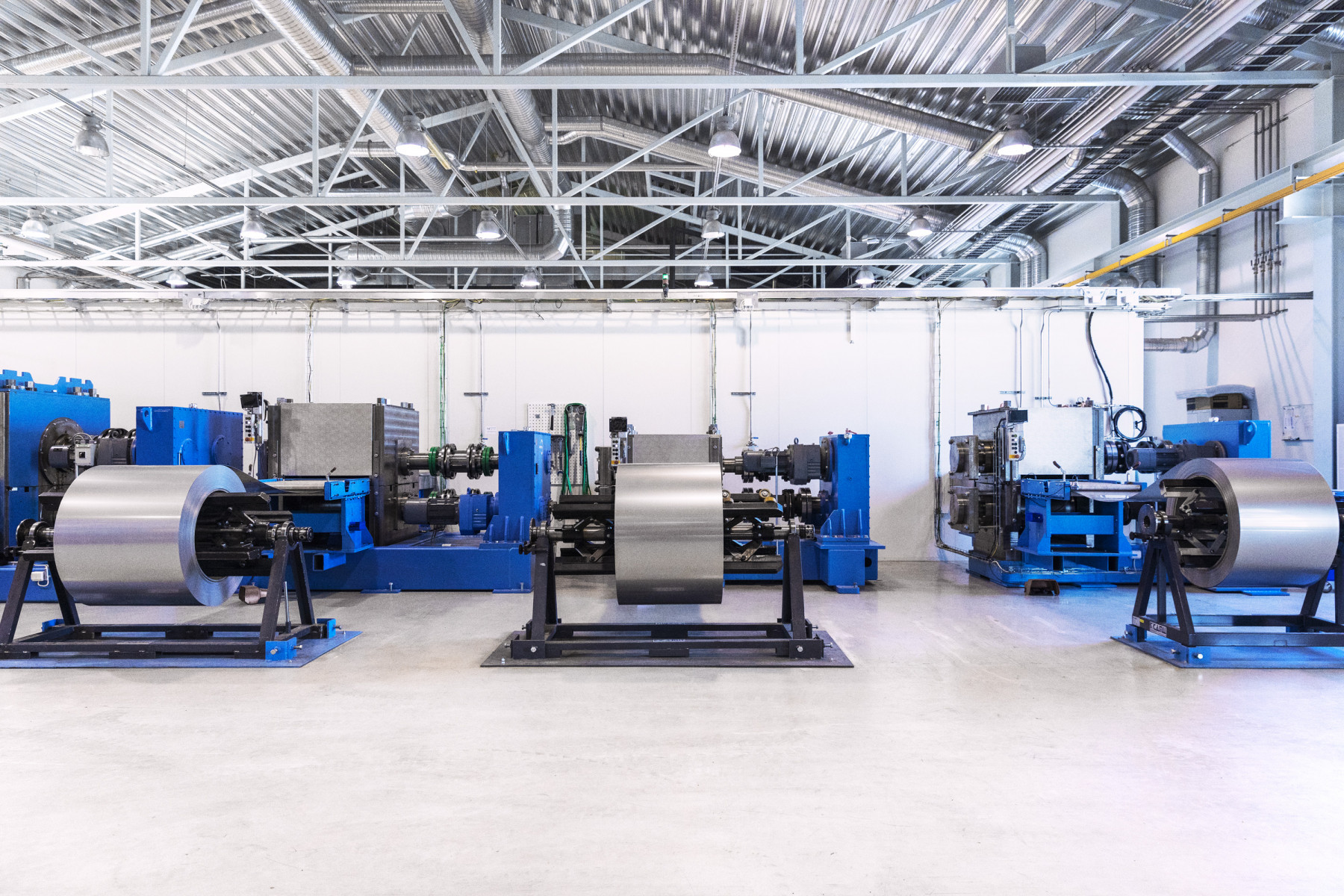
CONTACT
Let’s discuss hydrogen and heat transfer!
Would you like to know more about heat transfer? Want to talk or need help making decisions regarding your hydrogen process? Make sure you get in touch with Jeroen.
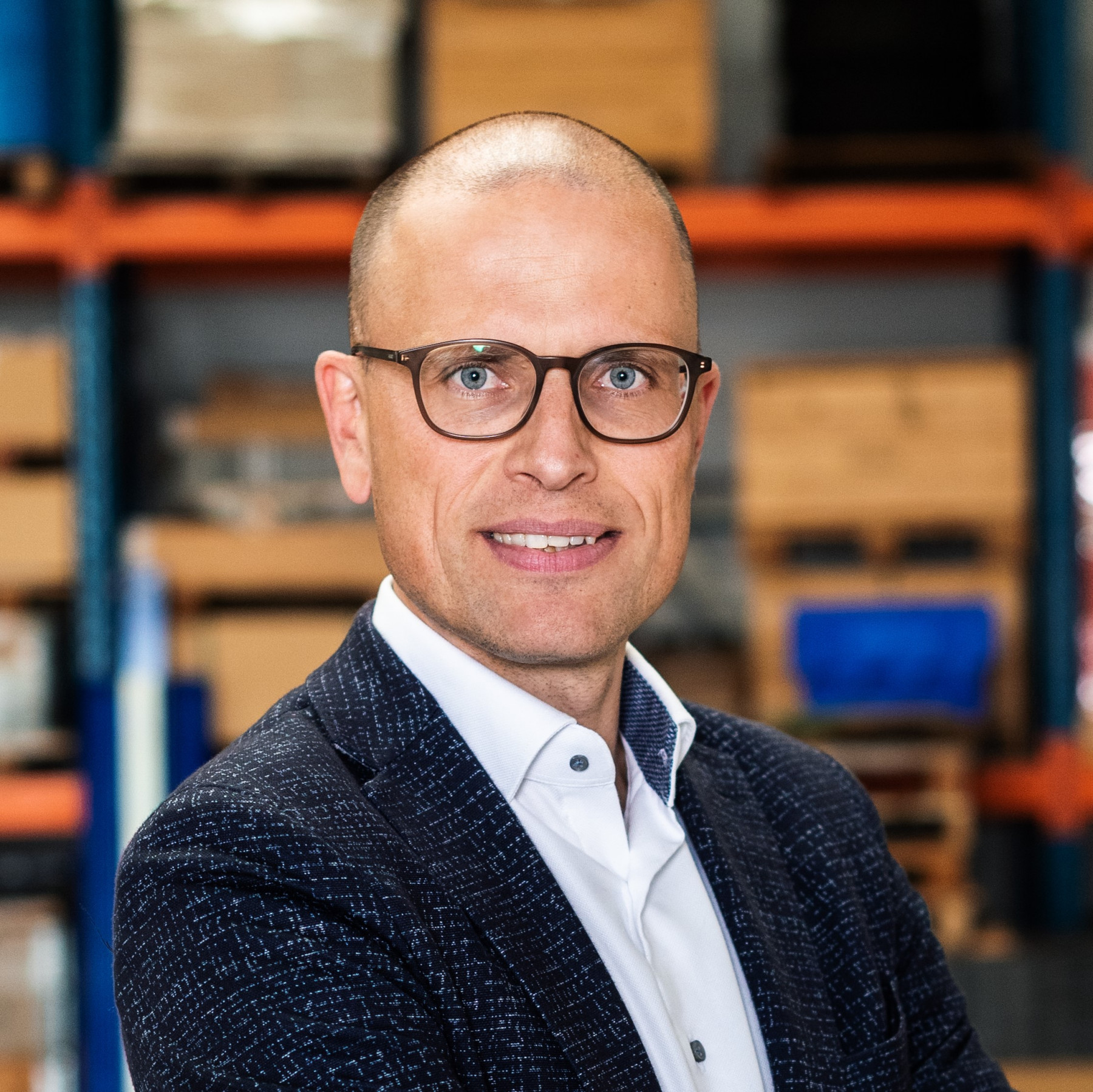