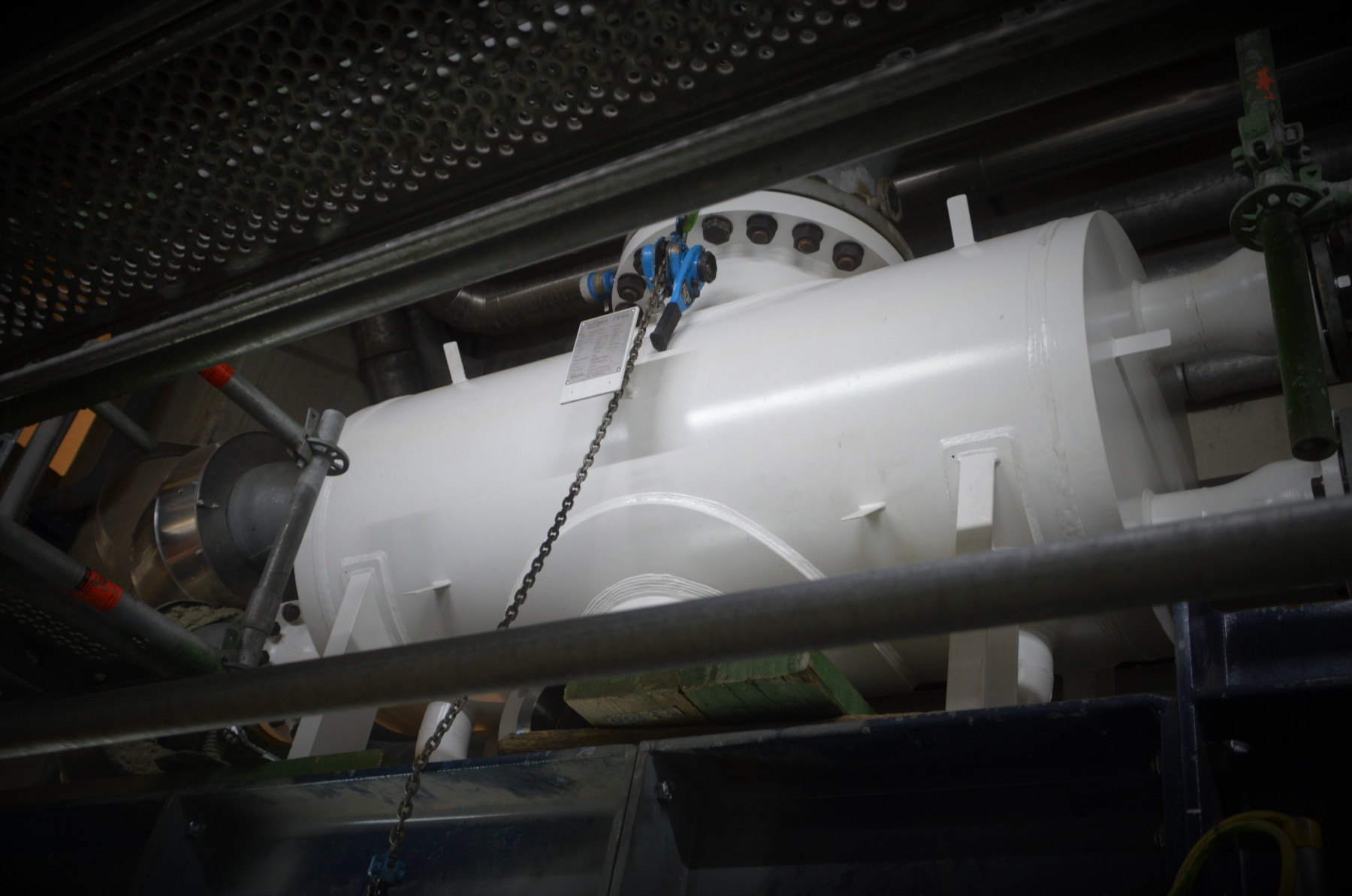
99% of our waste, re-used
At one of our clients, a waste energy company, 99% of the waste supplied is converted into sustainable energy and reusable materials. With this it contributes significantly to a cleaner society. The company processes 1.4 million tons of household and commercial waste, per year. After separating recyclable materials there is always residual waste. This waste is incinerated, which releases a lot of heat. Kapp supplied several Vahterus plate & shell heat exchangers, to be able to use the heat in the local district heating network.
For an optimal incineration process, it is important that waste has an even quality. That is why it is mixed in the waste boiler. Large grippers then throw the waste into the hoppers of the boilers. During incineration, the temperature fluctuates between 1000°C and 1200°C. This heat is re-used. Water in the walls of the boiler is exchanged by the heat, into steam. Thw steam is passed under high pressure through a number of turbines, which in turn drive a generator. This is used to supply 320 000 households, per year, with power.
There is still a lot of remaining heat, which is used for the production of district heating, enough for 30 000 households. Kapp’s heat exchangers come into play when decoupling the district heating network. In this situation, the heat exchangers are located directly at the decoupling, in the waste incineration plant (WIP). Here the temperatures are still quite high, just as the working pressure. That is why Kapp selected and supplied two Vahterus plate & shell heat exchangers for the application. This type of heat exchanger is compact, fully welded, has no gaskets and can therefore handle high pressures and temperatures. One is serving as a condenser and the other as a sub cooler.
After incineration, there is always residual material. We call this bottom ash. Our client recycles metals using special techniques. What remains after that is a valuable raw material for concrete and asphalt. The company also recycles raw materials such as gypsum and road salt, when cleaning the flue gases.
Hoisting and installing the heat exchangers was, and remains challenging, due to the limited available floor space and working height. The heat exchangers are currently being installed and are expected to be put in use in early September.