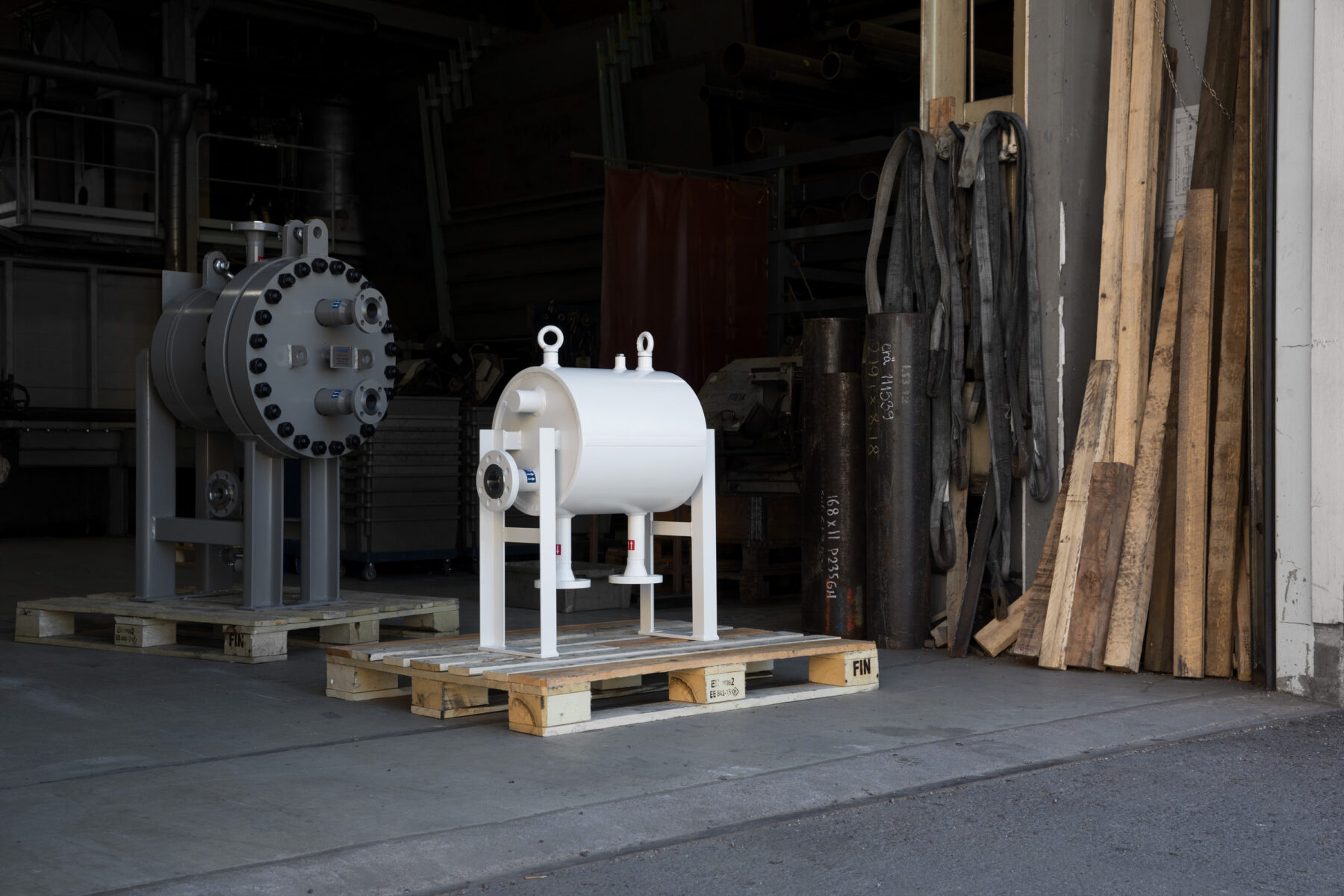
A sustainable and profitable approach to heat transfer in the process industry
In the process industry, we often tend to look for traditional heat transfer solutions that are not energy efficient. However, innovative heat exchanger solutions are sustainable and ensure business continuity. In addition, these solutions offer opportunities in other areas. Jeroen van Ruitenbeek, responsible for new energies at Kapp – Heat Transfer Engineers, shares his view on sustainable heat handling in the process industry.
“Organisations worldwide in the process industry that focus on making a great variation of products, energy carriers and fuels all face the same challenge to become more sustainable, but at different scales,” says Van Ruitenbeek. Within their processes where heat is required, heat is also released that is, unfortunately, lost unused. Energy-inefficient factories emit too much CO2. The amount of heat that is lost can be considerable, for example in processes for energy carriers such as ammonia and hydrogen. With the right solution, residual heat can be put to optimum use. “Innovative heat exchangers ensure that residual heat is put back into the production chain (circular) or is used for other purposes, such as district heating. “
The process industry faces other challenges as well. “In addition to the amount of unused heat, we also see challenges in meeting new regulations on CO2 emissions. To comply with the regulations, organisations must make site modifications within the physical limitations they have. The Netherlands has many factories that were built in the 1960s, 1970s and 1980s, all of which were built with little regard for energy efficiency,” Van Ruitenbeek says.
“Despite a wide-spread misconception, innovative compact heat exchangers do offer a solution. These compact heat exchangers, designed by our engineers and supplied in collaboration with various manufacturers, are designed to ensure business continuity in any process with a more sustainable and efficient approach than more traditional solutions, such as Shell & Tubes/tube exchangers. The ‘electrical heaters’ introduced by Kapp last year are prominent examples of sustainable solutions that also contribute to the electrification of the industry. “
But not every organisation can use the same heat exchangers. Van Ruitenbeek: “This is why it is important for us to find out what is needed within a specific process, so we can, without any obligation, provide advice on the right solution. In consultation with our engineers and manufacturers, we can determine how processes can be made more sustainable with the right compact heat exchangers, and how gains can be made in other areas as well.
With compact heat exchangers, space can be saved. Compact heat exchangers can be up to six times smaller and eight times lighter. Significant savings can be made in installation costs, for example for the foundation, insulation and pipework. In addition, innovative heat exchangers can recover heat with higher efficiency.
“At Kapp, we see it as our mission to accelerate the energy transition by fundamentally improving our clients’ processes and projects,” Van Ruitenbeek concludes.
