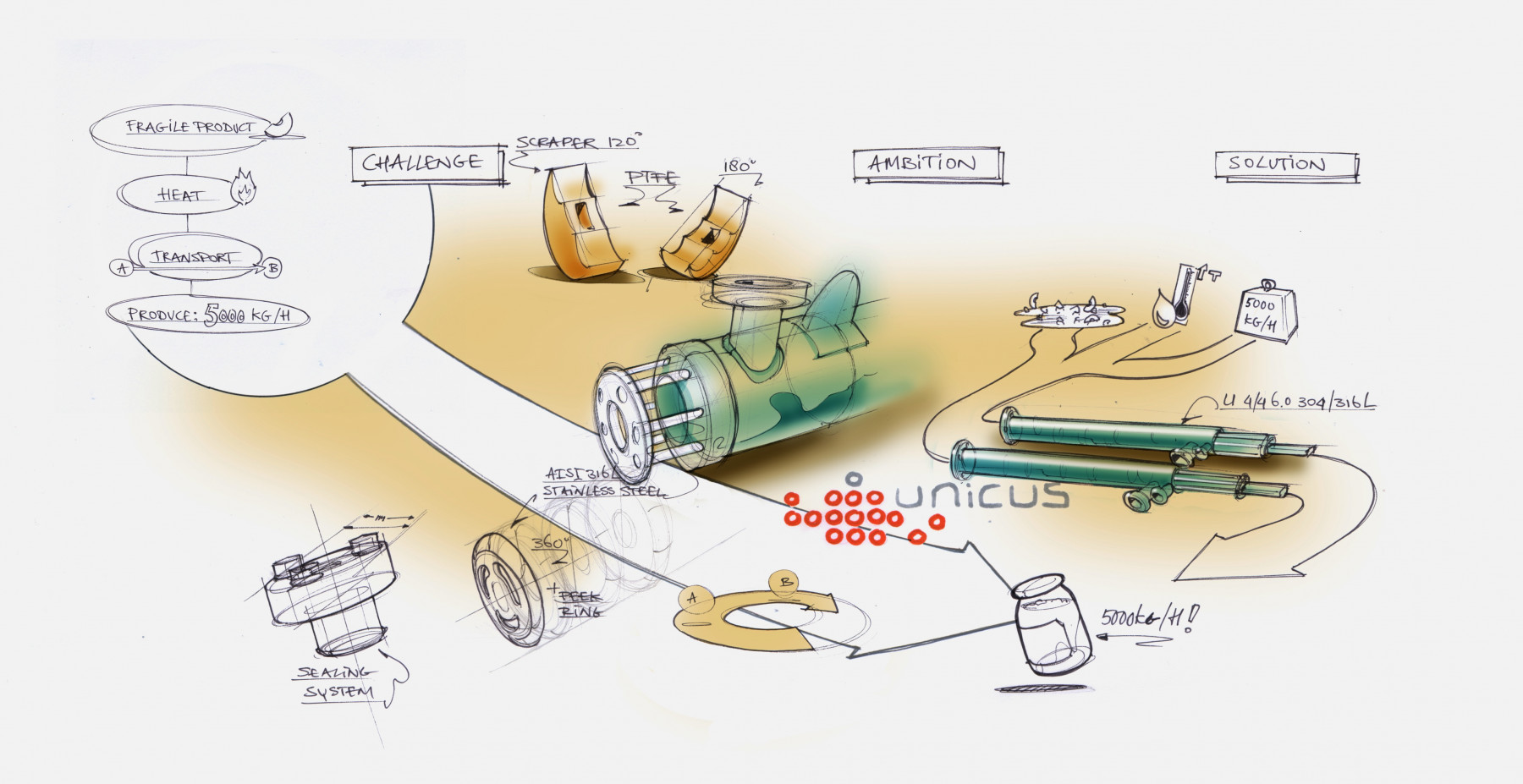
Apple sauce!
Probably the best-known side dish in the world, apple sauce has been packed in tins and glass jars for as long as we can remember. Now portion packing allows for a wider range of product varieties. New combinations of fruit – with and without chunks – are packed in small plastic cups. The manufacturer asked Kapp to design an installation that is able to heat the product to the right filling temperature.
The process
Pretty straightforward: people in the canning factory wash and cut the apples. They remove hard parts such as stalks. Putting the ingredients in the kettles should be done with great care; weight and timing are essential. Other fruit varieties can be added. The apple sauce then goes through pipes to the filling installation. Here, the product is heated until it reaches the right filling temperature, which in this case is equal to sterilization temperature. The hot mix is pumped inside the filling machine, which moulds, fills and seals the plastic cups with apple sauce. A cooling line reduces the heat of the product to room temperature.
The project
Heating the product before packing was Kapp’s assignment. Ordinary heat transfer installations were unsuitable because of the viscosity and chunky properties of the apple sauce. We chose to apply a dynamic scraped surface heat exchanger by Unicus. This type of machine is self-cleaning and produces an increase in turbulence due to the continuous reciprocating movement of the scraping elements. Two serial units heat the product using hot water. Steam was not possible because the client is very specific about the maximum temperature. The unit was designed with minimal damage to the product – either thermally or mechanically – as one of the main objectives. Special configurations were applied in order to enable the chunks of fruit to pass the scrapers. The capacity of the installation is 5.000 kilos of chunky apple sauce per hour.
The choice
Because the use of an installation in a similar environment is quite innovative, we first had to perform a pilot test in order to find out whether it was achievable. The client demanded no loss of weight in the fixed parts, as little thermal pressure on the product as possible and a drainable unit. They got exactly what they needed: a scraper unit with low thermal and mechanical pressure and very little loss of pressure in the product stream. Simply a matter of smart designing… Kapp was awarded the assignment because of our flexible attitude, our superior solution and the right balance between price and technique. The installation has been supplied by HRS Heat Exchangers in Spain.
Scraped surface heat exchangers do need care on a regular basis. The units will be cleaned by means of a CIP cycle. Because the moving parts move relatively slowly and are easily accessible, the cost of maintenance remains low.