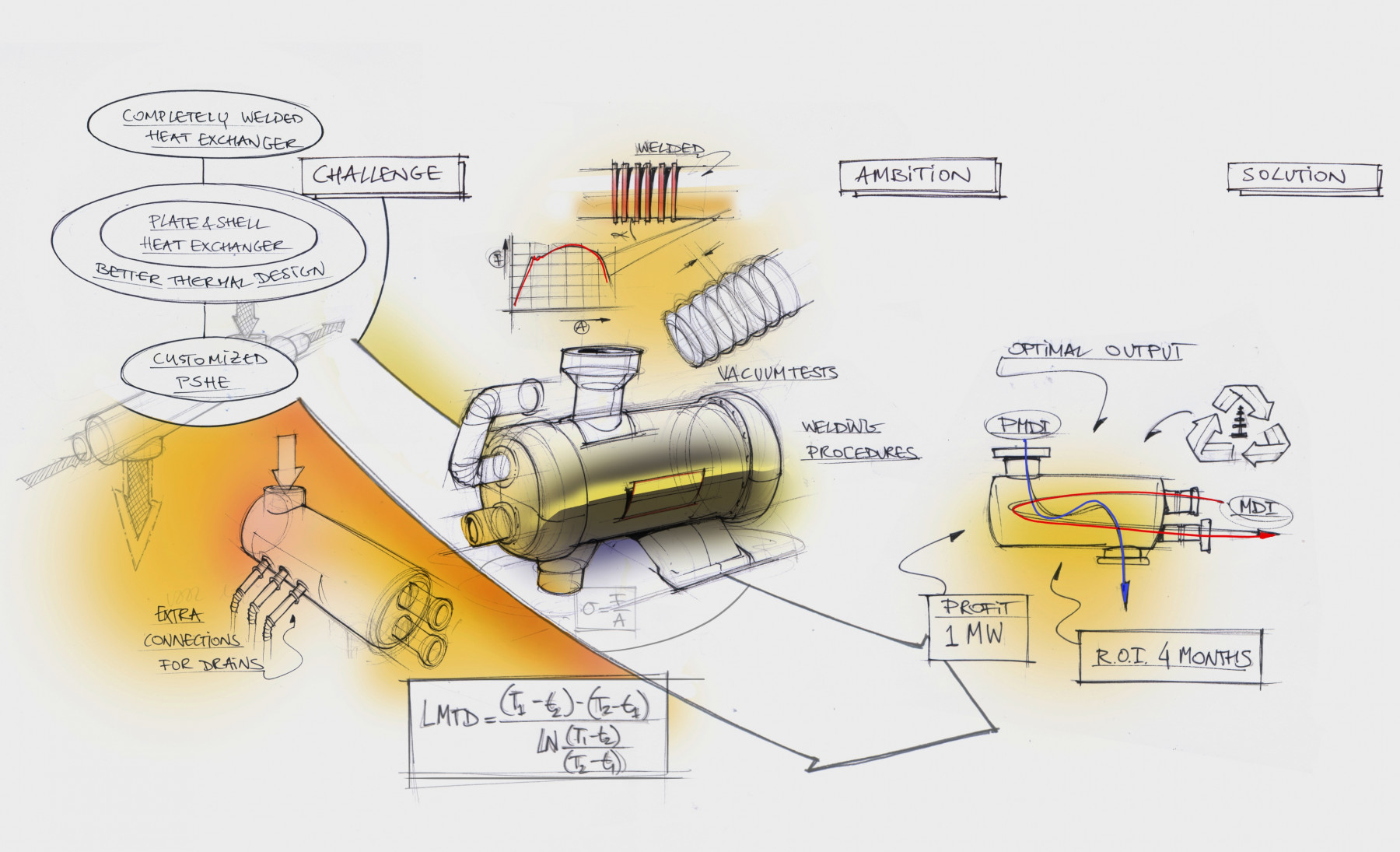
Foam!
In a world struggling with environmental issues, recycling energy is not only a matter of common economics, but also one of common decency. The leading manufacturer of polyurethane foams asked Kapp if we were able to use the heat of one product flow cooling down as a source to heat up another product flow. We were!
The process
MDI, TDI and Polyols are urethane chemicals. Polyurethane is only a household word, since it applies to a large number of polymers. Their versatility makes them suitable for various applications such as lightweight, rigid foams, soft flexible foams and dense, solid composites. MDI is widely used in a range of markets such as automotive, furniture, construction, appliances, insulation and recreation.
The project
As in almost every factory where chemicals are produced, the risk of hazards must be eliminated at every stage. That is why we initially thought of a completely welded heat exchanger. Eventually, we opted for a plate exchanger with a welded plate package only, because it responds better to the desired thermal design with its relatively low LMTD.
The choice
In its current function, the exchanger uses a flow of MDI, which is to be cooled down, in order to heat a flow of PMDI. The resulting regenerative power is 1 Megawatt. We calculated that the exchanger will recoup its investment within 4 months of continuous service, which convinced the customer to choose for Kapp. The customer was very specific about:
- High PED-class
- Vacuum tests
- Non-destructive tests
- Strength calculations
- Welding procedures
- Extra connections for drains