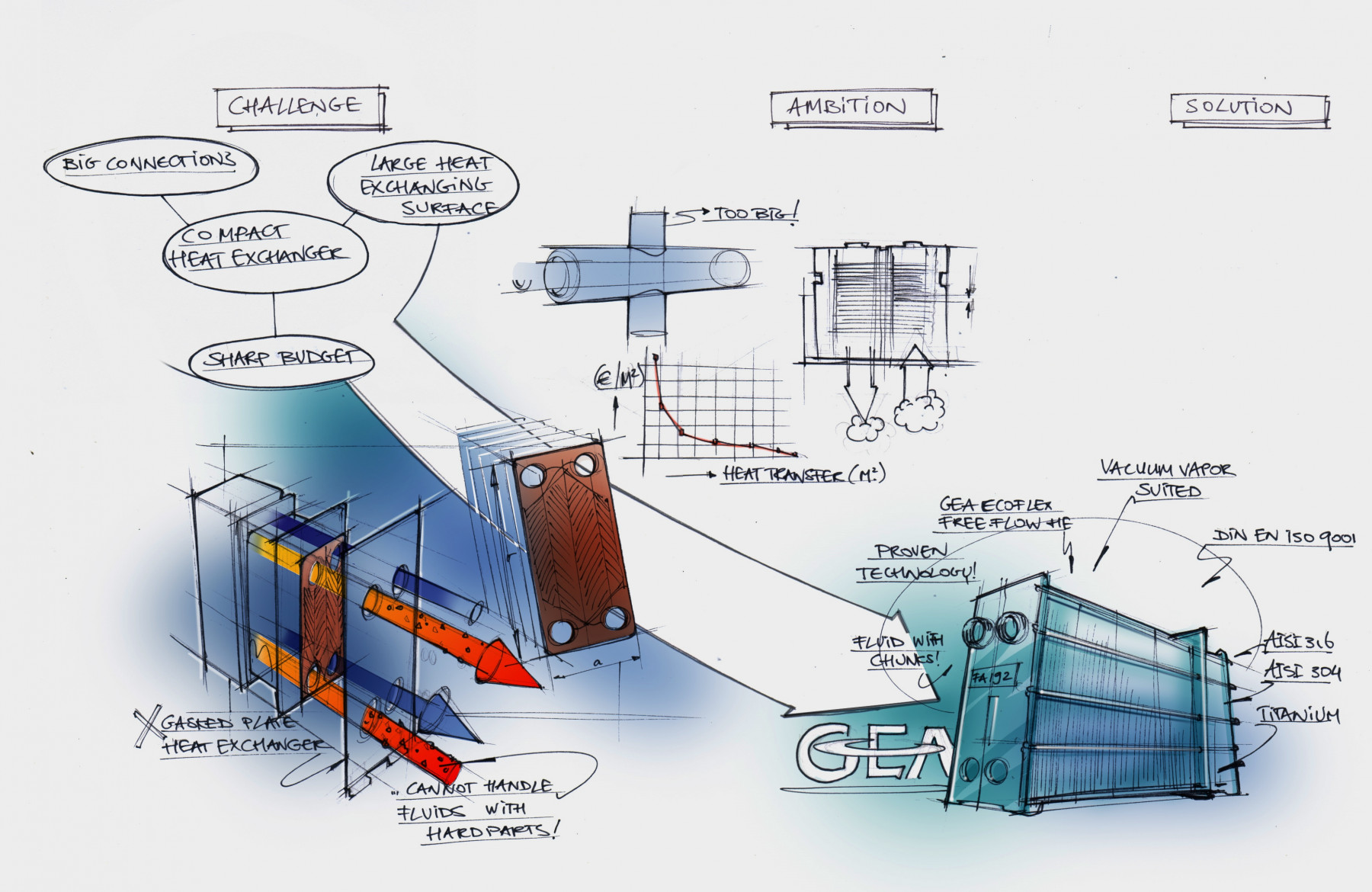
Sugar!
The sugar beet is in peril. Within the European Union, sugar production is subsidised in order to ensure the continued existence of the European sugar industry. For the sake of fair competition with other sugar-producing communities such as those in Africa and South America, support will be reduced during the next couple of years. This has led to the consolidation of several large sugar producers and to an increase in technological innovation: each year, the industry squeezes more sugar out of the sugar beet. In the factories, no effort is spared to reduce production costs, and from the point of view of energy consumption, the European sugar industry is the most efficient in the world. No one uses less energy per kilogramme of sugar. This is achieved for a large part by re-using energy from waste heat, and one sugar factory asked Kapp to help them. Now isn’t that sweet?
The process
The beet are washed, cut and heated. Protein is separated from the raw sugar juice, after which it is filtered and heated up even further in order to cause water in the juice to evaporate. This process raises the sugar concentration, eventually causing it to turn into the crystallized sugar that is familiar to us.
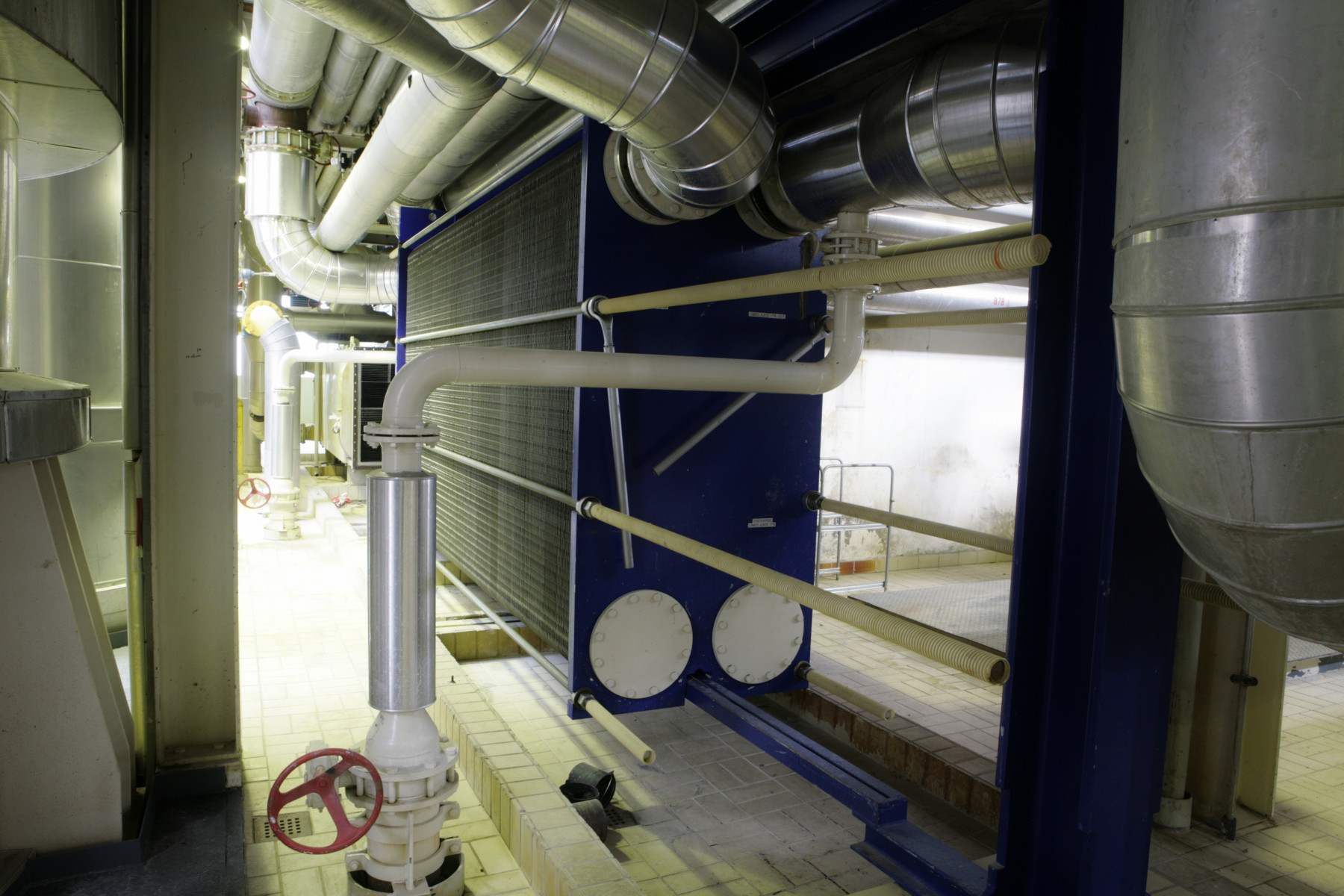
The project
Heat exchanging is a well-known technique in the sugar business. In the past, however, no one believed that it would be possible to re-use the heat from every step in the production process. Take for example the residual vapour from the crystallization process. Its temperature will always remain below 100 degrees Celsius. We call this vacuum vapour, because under normal pressure, vapour of this temperature would condense. Vacuum vapour contains a lot of heat, but takes up a huge volume, which makes it hard to design a heat transfer installation with enough capacity. In addition, the temperature of the vapor is quite low: you can only use it to heat sugar juice with an even lower temperature, and only raw sugar juice has a lower temperature. In order to work profitably, you would need an installation with a high heat transfer rate, able to perform well even with low differences in temperature.
The choice
Our client opted for a relatively compact installation with large connections on the vapour side and a large heat-exchanging surface that can handle vacuum vapour under all conditions. And all this had to be done within a tight budget, of course. A conventional tube heat exchanger was out of the question, because it would have had to be enormous to take into account the low temperature gradient. A traditional gasket plate heat exchanger was not suitable either, because it cannot handle fluids containing solids (like raw sugar juice, which contains bits of beet and sand), since the plates have points of contact. We found an alternative in the Kelvion (formerly GEA Ecoflex) free-flow heat exchanger. It does have gaskets, but no points of contact and is therefore suitable for the purpose. In fact, this installation was designed especially for the handling of raw juice in the sugar industry, but had never been used in combination with vacuum vapour. Together with Kelvion PHE, we designed a custom version for the job: the Kelvion Free-flow Heat Exchanger, This decision allowed us to:
- stay within budget
- use proven technology
- produce a construction that was compact and modular
- handle vacuum vapour