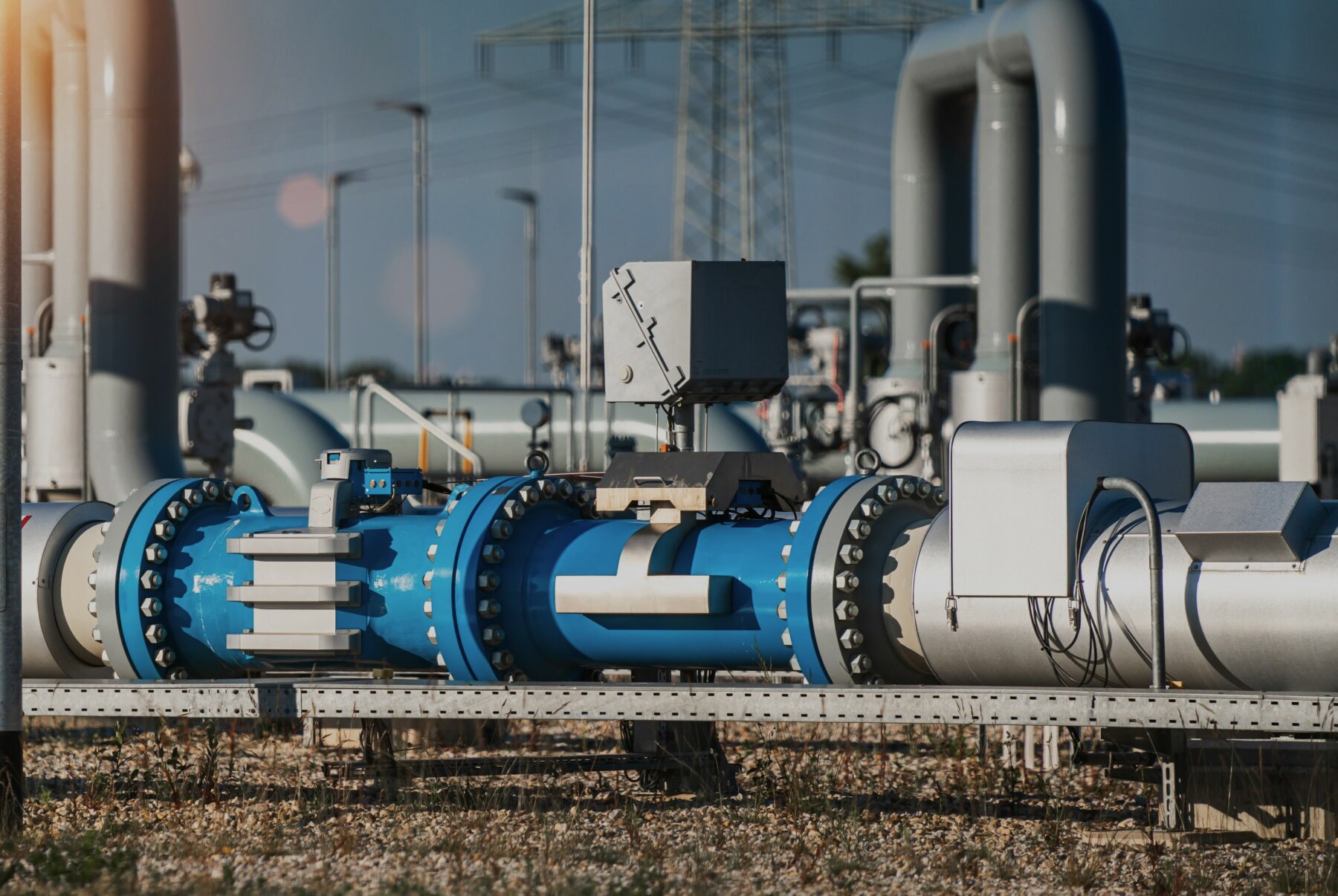
NOTRE MISSION
Hydrogène et transfert de chaleur, inextricablement liés
Nous sommes convaincus, comme vous probablement, que l’hydrogène vert apportera une contribution majeure à la transition énergétique. Les développements dans le domaine de l’hydrogène sont fulgurants, le nombre d’installations et d’électrolyseurs augmentant rapidement dans le monde entier. Mais les processus ne sont pas encore totalement cristallisés. Et c’est compréhensible ! Partout dans le monde, on cherche la configuration optimale pour produire de l’hydrogène de la manière la plus durable et la plus efficace possible. Dans le domaine du transfert de chaleur, Kapp connaît la voie à suivre et nous disposons d’un échangeur de chaleur adapté à chaque étape de la production d’hydrogène. Cela nous donne un avantage réel, qui profite à nos clients. Mais la connaissance et l’expérience d’autres experts de l’industrie de l’hydrogène sont essentielles pour nous. Notre approche sur ce marché est donc : “Ici pour enseigner, ici pour apprendre “. Cette philosophie découle de la prise de conscience que le temps est compté et que nous pouvons accélérer les développements ensemble en collaboration avec d’autres experts du secteur.
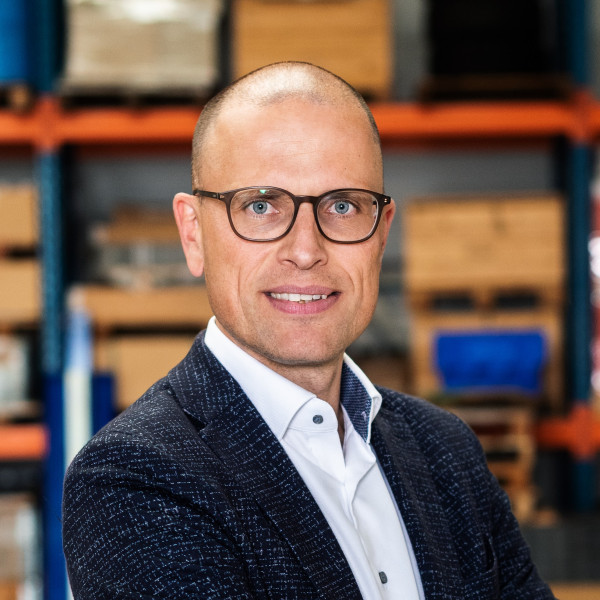
Notre approche sur ce marché est donc : Ici pour enseigner, ici pour apprendre.
JEROEN VAN RUITENBEEK – General Manager Kapp
NOTRE ENGAGEMENT
NOS SOLUTIONS
Nous pouvons améliorer votre processus de production d’hydrogène
La production d’hydrogène vert nécessite une électricité générée de manière durable. C’est dans cette optique que nous nous attaquons aux défis du processus de production d’hydrogène. Les échangeurs de chaleur sont utilisés à chaque étape du processus de production d’hydrogène. Nous connaissons bien les processus, les défis associés et les solutions. Pour chaque étape, nous disposons d’un échangeur de chaleur adapté. Et dans les sous-processus de compression et de purification, nous avons tout simplement un avantage unique avec un échangeur de chaleur très compact. Nous serions ravis de vous informer plus à ce sujet.
NOTRE UNICITÉ
La meilleure solution pour le processus de production d’hydrogène
L’hydrogène est la plus petite molécule. Lors de la production d’hydrogène, cela comporte des risques. Dans certains processus de production d’hydrogène, les pressions sont élevées et les fuites peuvent être désastreuses ; les flux d’hydrogène et d’oxygène présentent un risque d’explosion. Dans des processus aussi critiques, disposer du bon équipement est vital. Pour les processus de production d’hydrogène, les grands échangeurs de chaleur à tubes traditionnels sont encore souvent envisagés en raison de leur solidité. Parfois, c’est la bonne solution, mais plus souvent, d’autres techniques sont mieux adaptées. Et il existe de nombreux exemples où notre échangeur de chaleur à plaques entièrement soudées est pratiquement la seule solution appropriée. Dans certains cas, nos solutions pèsent 70 % de moins, coûtent 50 % de moins, récupèrent plus de chaleur et sont au moins aussi solides que l’échangeur de chaleur à tubes traditionnel. Pour un certain nombre de processus de production d’hydrogène, un échangeur de chaleur à plaques et à coques est la technique parfaite, et dans certains cas la seule appropriée. Un échangeur de chaleur à plaques et à coques est :
- très compact, donc plus petit, ce qui implique moins de travaux de génie civil, d’isolation, de tuyauterie, etc. ;
- adapté aux pressions élevées ;
- entièrement soudé, et donc sûr pour l’application de l’hydrogène et garanti sans fuite ;
- plus rentable grâce à des coûts d’investissement et d’exploitation réduits.
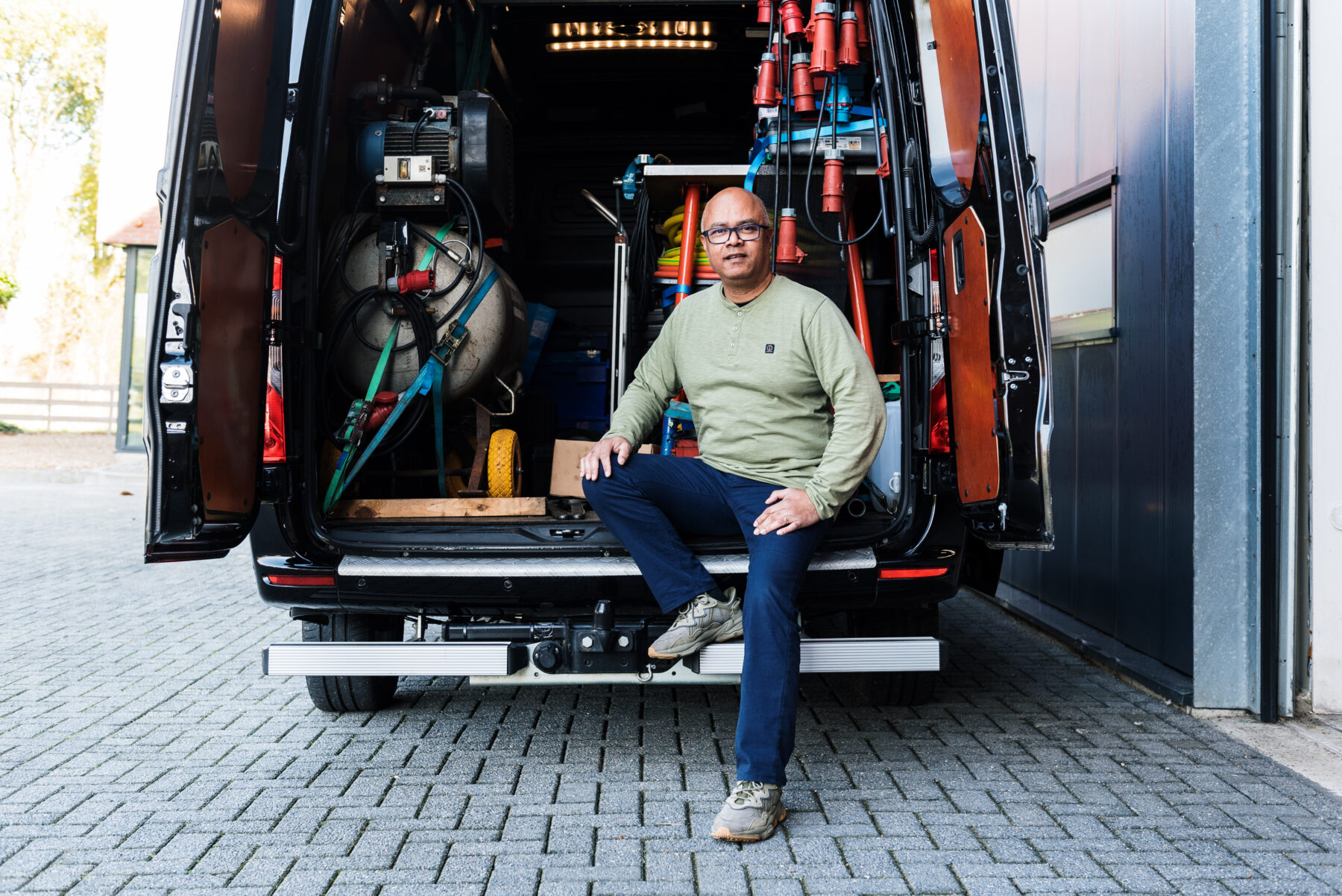
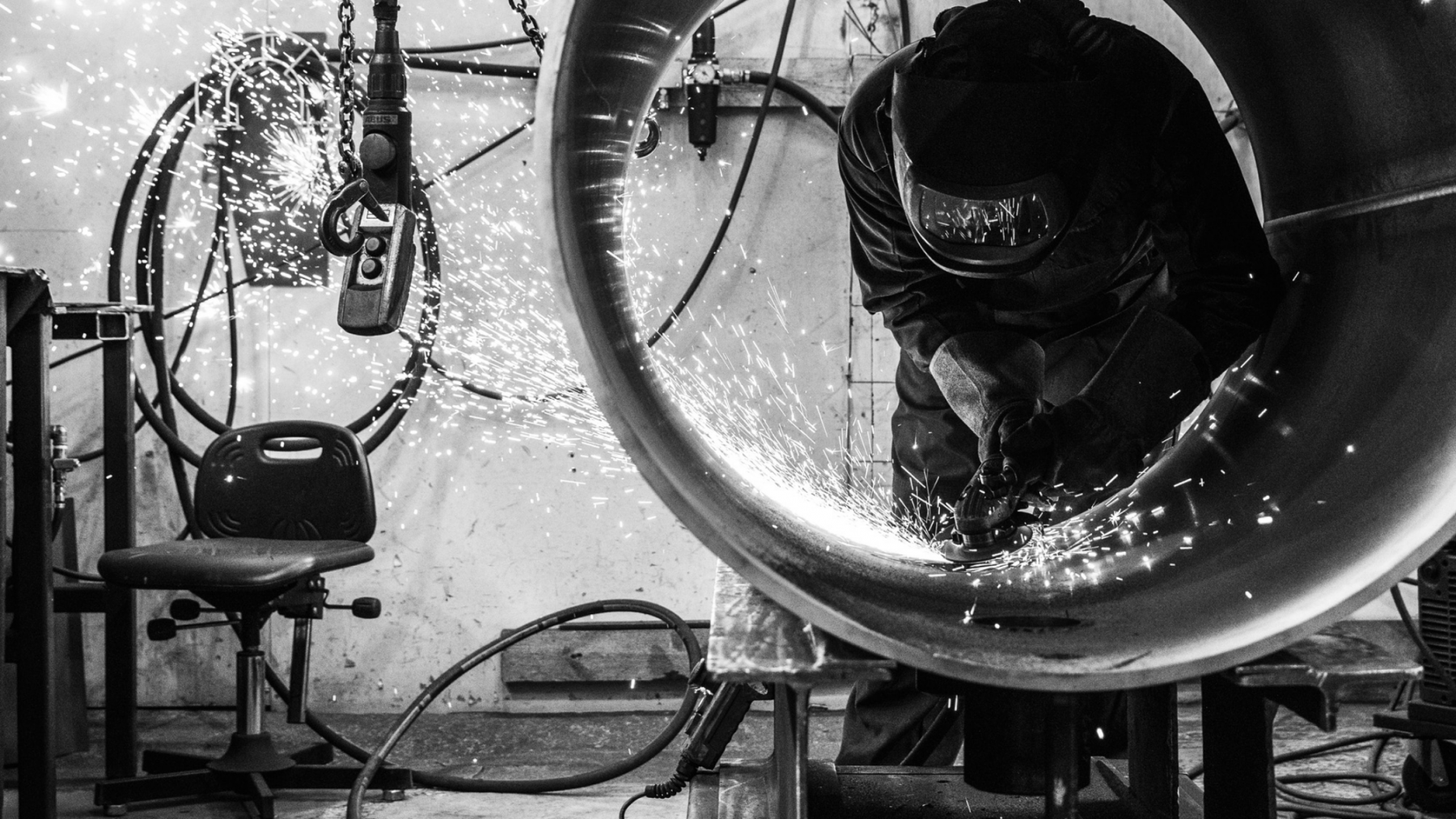
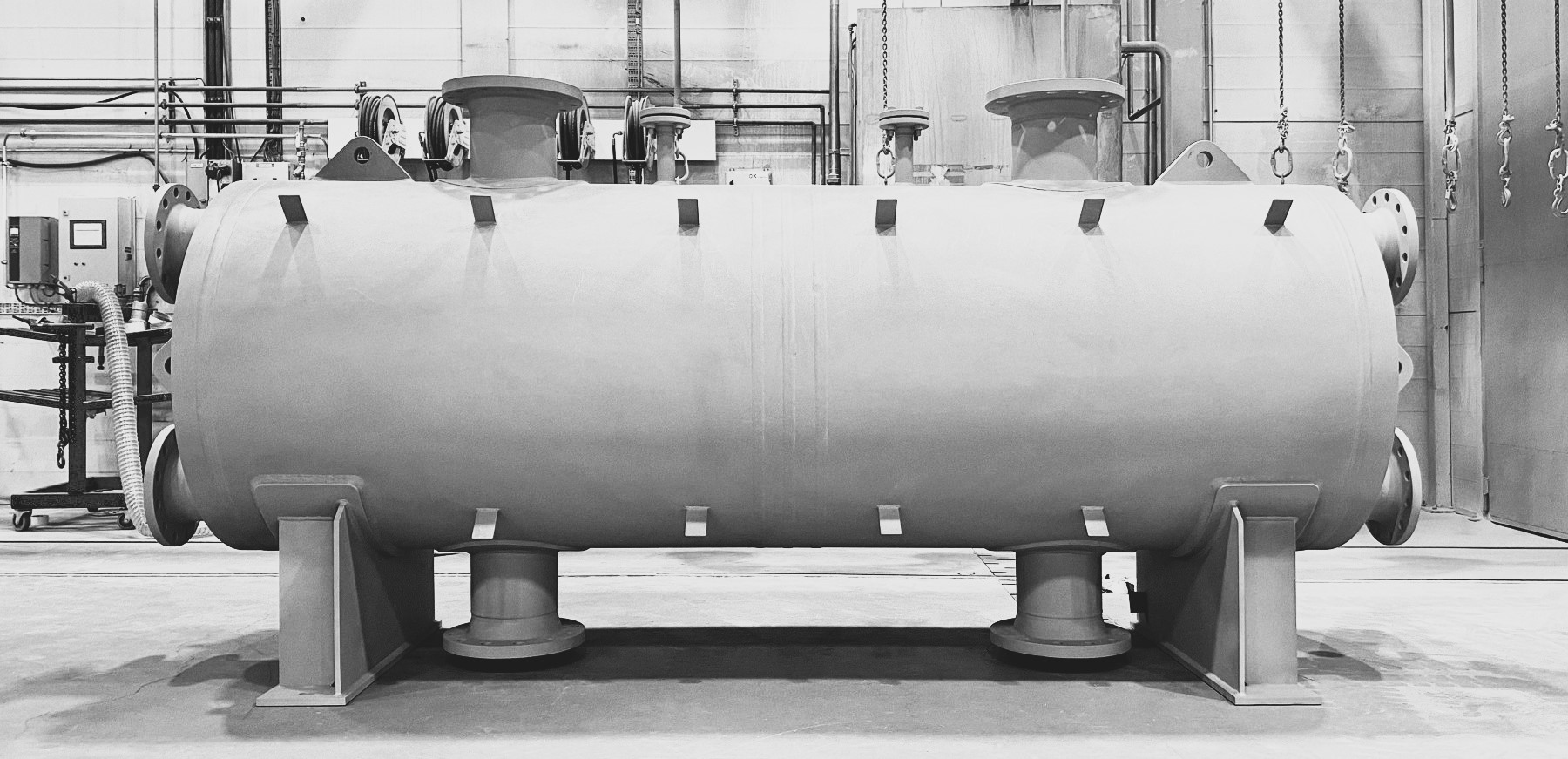
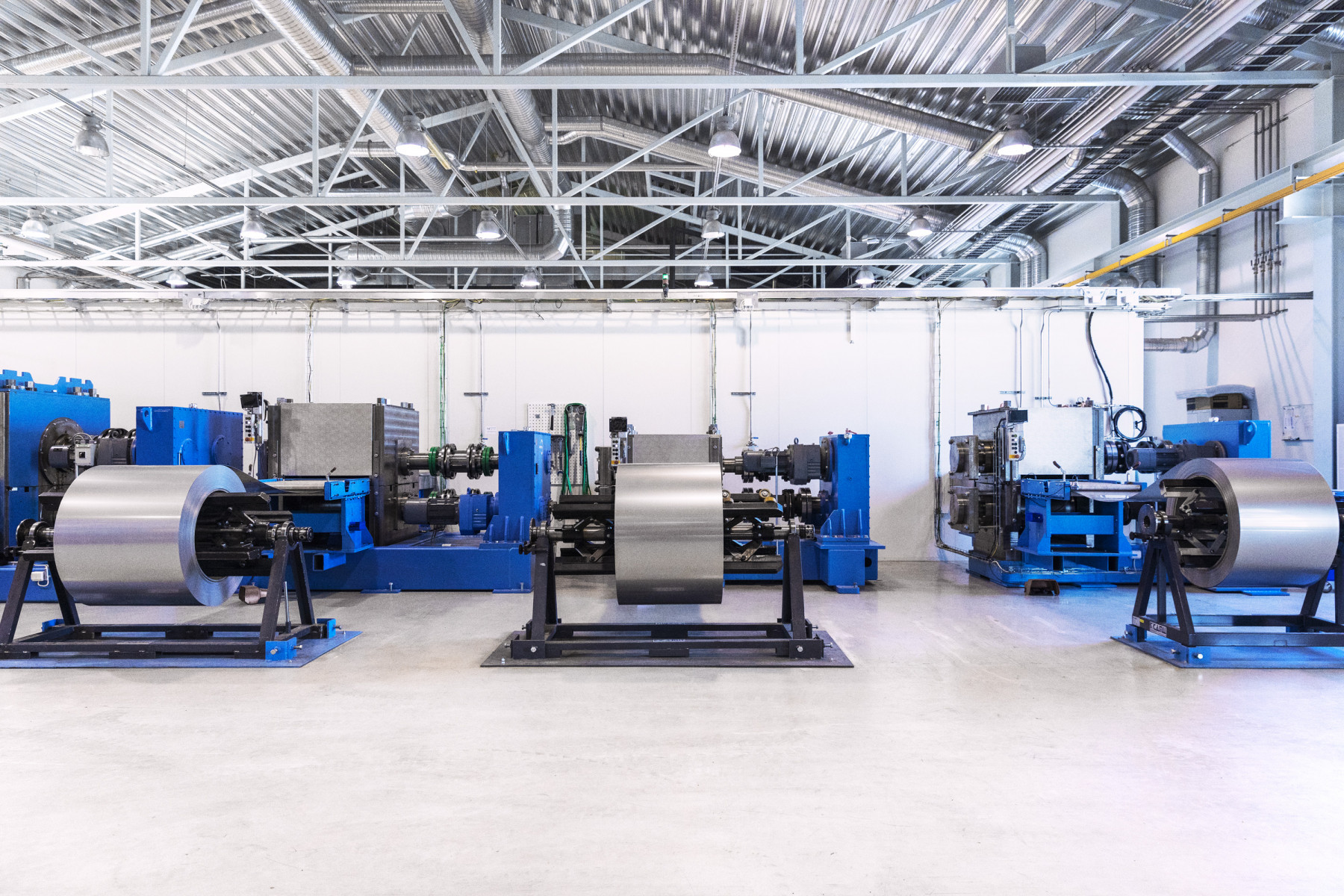
CONTACT
Vous souhaitez parler d’hydrogène et de transfert de chaleur ?
Vous souhaitez mieux comprendre le transfert de chaleur ? Vous souhaitez en discuter ou vous avez besoin d’aide pour prendre des décisions concernant votre processus d’hydrogène ? Contactez Jeroen.
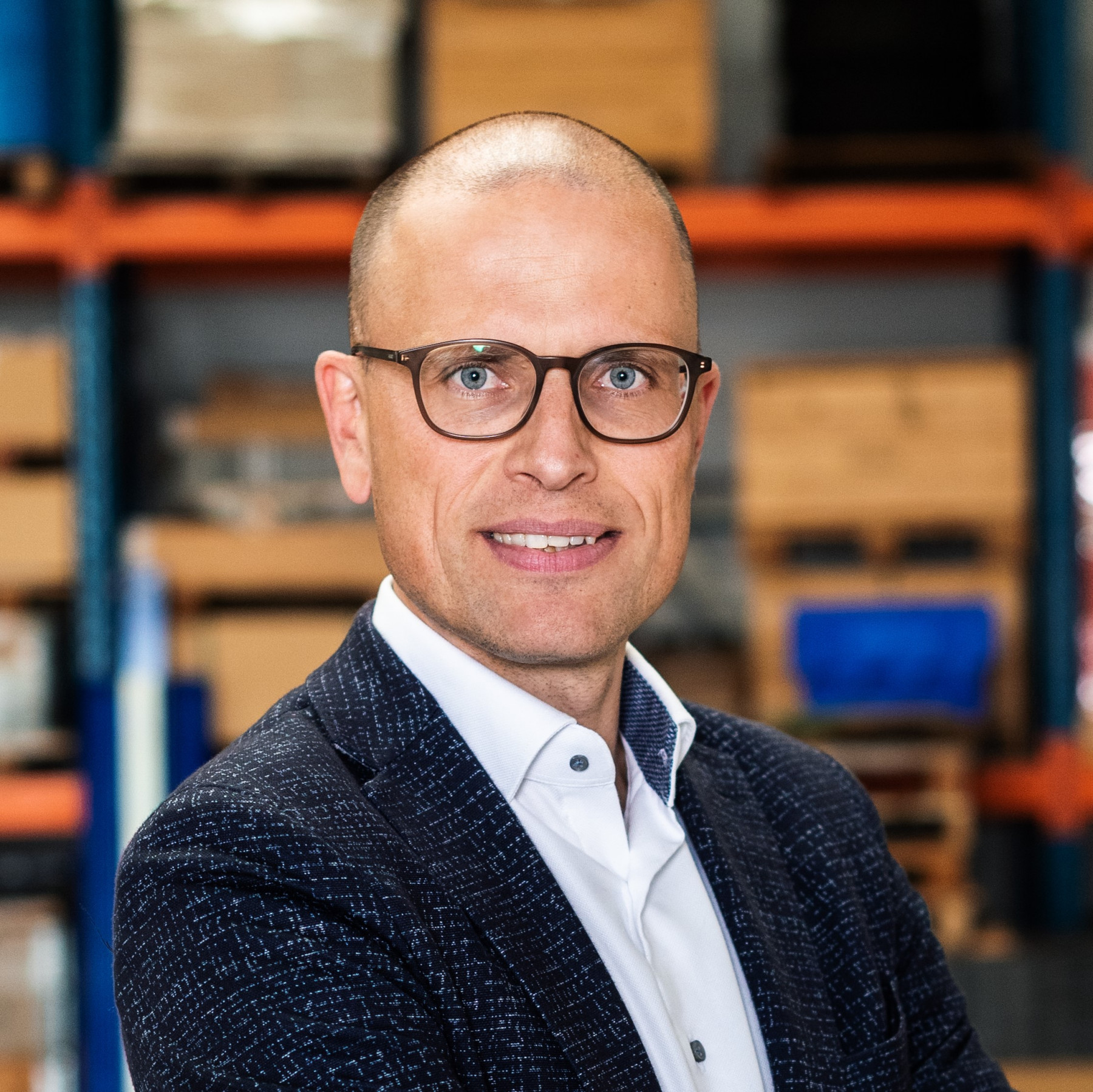